El Inconel 718 es una superaleación base níquel que ha transformado múltiples sectores industriales gracias a su capacidad para operar en condiciones extremas. Este material combina una resistencia térmica excepcional con propiedades mecánicas sobresalientes, lo que lo hace ideal para aplicaciones críticas en las industrias aeroespacial, automotriz y de generación de energía. Pero trabajar con él no es tarea fácil. En este artículo, exploraremos las características únicas del Inconel 718, sus principales aplicaciones y por qué su máquina presenta un reto significativo.
¿Qué hace único al Inconel 718?
-
Resistencia térmica y mecánica:
- Mantiene su estabilidad estructural incluso a temperaturas de hasta 700°C, lo que lo convierte en un material de elección para turbinas de gas y motores de alto rendimiento.
-
Resistencia a la corrosión:
- Su composición rica en níquel y cromo le permite resistir ambientes hostiles, como los que se encuentran en la industria química o marítima.
-
Alta resistencia a la fluencia y la fatiga térmica:
- Esta superaleación soporta cargas mecánicas y térmicas prolongadas sin perder sus propiedades, una característica crucial para aplicaciones de alto estrés.
-
Baja conductividad térmica:
- Aunque es una ventaja para su desempeño a altas temperaturas, esta característica complica su mecanizado, ya que el calor generado en el corte se transfiere a la herramienta en lugar de disiparse a través de las virutas.
Aplicaciones clave del Inconel 718
El Inconel 718 se utiliza en una variedad de aplicaciones donde otros materiales no son viables:
- Industria aeroespacial: Álabes de turbina, componentes de motores a reacción y sistemas de escape.
- Industria automotriz: Partes de turbocargadores sometidos a altas presiones y temperaturas.
- Industria de generación de energía: Cámaras de combustión y componentes en turbinas de gas.
- Sector químico: Equipos resistentes a la corrosión, como intercambiadores de calor y reactores.
¿Por qué su mecanizado es un desafío?
Aunque el Inconel 718 no es particularmente duro (alrededor de 45 HRC en su estado tratado térmicamente), su mecanizado presenta varios desafíos únicos:
-
Generación excesiva de calor:
- Su baja conductividad térmica provoca una acumulación significativa de calor en la herramienta, aumentando el riesgo de desgaste y deformación.
-
Endurecimiento por deformación:
- Durante el corte, el material tiende a endurecerse, lo que complica los pasados posteriores y requiere herramientas robustas.
-
Propiedades abrasivas:
- Los carburos presentes en su matriz aceleran el desgaste de las herramientas.
-
Adherencia del material:
- La alta cantidad de níquel provoca que el material se adhiera al filo de la herramienta, afectando el acabado superficial y reduciendo la vida útil de la herramienta.
La solución: Herramientas especializadas de CERATIZIT
Dominar el mecanizado del Inconel 718 requiere herramientas diseñadas específicamente para superar estos retos. La MonsterMill NCR de CERATIZIT es una solución avanzada que combina:
- Recubrimientos resistentes al calor, como Dragonskin , para prolongar la vida útil de la herramienta.
- Geometría de corte optimizada para minimizar el calor y las fuerzas generadas.
- Estabilidad mejorada gracias a un núcleo reforzado.
Estas características permiten abordar el mecanizado de Inconel 718 con confianza, logrando alta precisión y productividad.
Conclusión
El Inconel 718 es un material extraordinario que impulsa las innovaciones en industrias críticas. Sin embargo, su mecanizado requiere una combinación de estrategias avanzadas y herramientas especializadas. Con soluciones como la MonsterMill NCR de CERATIZIT , es posible superar estos desafíos y aprovechar al máximo este material único.
🔗 Explora nuestras soluciones para el mecanizado de Inconel 718 en CERATIZIT.
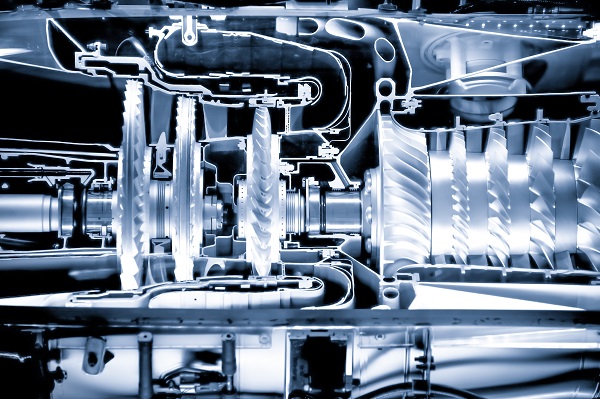